The Steerprop azimuth propulsors are designed and tailor-made to meet the most stringent of customer needs. How can a customer be assured that the overall quality and purchased equipment fulfil the contractual requirements? The answer is Steerprop’s comprehensive and unique Factory Acceptance Test. “Our value adding concept is that we test not only the propulsor, but we pre-assemble the propulsor and all components such as the control system, lubrication system, panels and displays before we test the whole package”, says Esa Peltomaa, Electrical and Automation Manager at Steerprop.
Before any equipment or products leave the factory, they all go through the process of Factory Acceptance Tests (FAT). The purpose of a FAT is to verify for the customer and classification society, as well as the manufacturer, that the ordered equipment meets the contractual requirements and functions as expected.
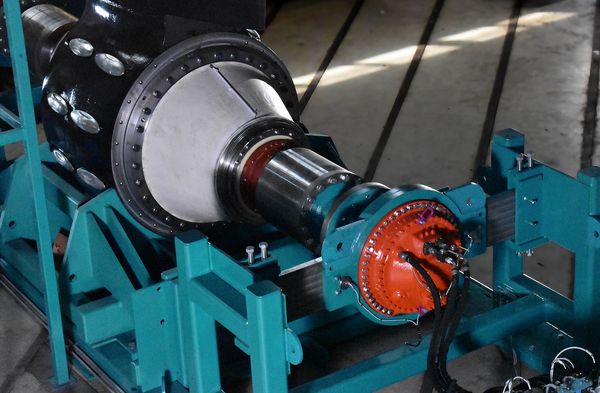
Reducing the number of installable components
It is rather usual that solution providers in the propulsor industry deliver a large number of separate components, which then require extensive cabling and installation work on site. Furthermore, a complicated installation can have a negative impact on commissioning time. “In our workshop we have a full torque test bench where we perform the factory acceptance testing of the complete solution, also when the propulsor control system is built into one pre-tested assembly that minimises the installation and commissioning work”, says Mr Peltomaa.
“When the propulsor control system is built into one pre-tested assembly that minimises the installation and commissioning work.”
Steerprop’s FAT-concept is a cost-effective solution for the customer and detects any functional issues before the propulsor and equipment arrive at the shipyard for installation. Fixing potential issues while the equipment is still at the factory has a positive impact on the timeline and budget, for example. “When the propulsor and control system are pre-assembled and tested together at our factory, we can verify that everything works as a complete product before sending it to the shipyard. This ensures a simpler installation with fewer risks for errors”, says Mr Peltomaa.
Shortening the commissioning time
The FAT test program is based on the agreement, technical specifications and other documents relating to the project characteristics.
A FAT brings several advantages for both parties. The manufacturer can guarantee that the equipment is operational and the customer can verify the equipment against the contract specifications. Other additional benefits include the possibility for customers to “touch and feel” the equipment in operational mode before delivery, and to have an opportunity to get some preliminary hands-on training.
“An advantage for the customer is that this procedure shortens the time needed for commissioning and minimises the risk for errors.”
Steerprop’s FAT concept with everything in one “package” makes it easier to solve potential problems and fault situations instead of just having separate components interconnected. The cabling between the propulsor and the control system is done with ready-made and pre-tested plug cables. “An advantage for the customer is that this procedure shortens the time needed for commissioning and minimises the risk for errors. A Steerprop commissioning takes 1-2 weeks plus sea trials. In addition to the test protocol and a number of classification certificates, our customers receive a product of enhanced quality as a result of our FAT concept”, says Mr Peltomaa.
FAT from your office – Online
All FAT inspections and testing are made at the manufacturer’s test facilities in Finland. The global pandemic, though, made it difficult, not to say impossible, for customers to attend a FAT on location. Steerprop, however, found a solution to this challenge and successfully implemented a system through which customers can follow the FAT online via a remote connection.
“The online FAT is an option we offer customers that prefer not to travel regardless of if there is a pandemic or not. The online FAT saves both time and money for customers as they do not have to travel to be on site. So far, the response has been positive and we expect this trend to continue. We are still in the quite early stages of this method and aim to improve it substantially, Mr Peltomaa concludes.
Author