When designing and dimensioning propulsors for optimal performance and fuel efficiency in arctic operations, it is crucial to understand how ice loads affect the vessel and the propulsor. It is also important to understand the requirements of each ice class. We at Steerprop have substantial experience and expertise in developing propulsion solutions for arctic operations, in fact, every third icebreaker in operation around the world relies on Steerprop technology.
How to best dimension every propulsor depends on the requirements of each ice class. To ensure the best results when designing each propulsor, it is important to check all classification requirements for that vessel. The ice class rules for arctic vessels in most class societies follow the IACS Unified Requirements for Polar Ships, with PC 1 being the hardest ice and PC 7 being the weakest – old ice is, in general, harder than new.
The nature of the ice, and how much pressure is required to break through, affects the load, so it is vital to understand how ice load affects the propulsor under the water. The class rules dictate how to dimension the housing to break through different ice load magnitudes. For example, the longitudinal load is factored differently than the transversal load, which is more critical with respect to the propulsor design. Still, both must account for the load of a consolidated ice sheet that slides down the hull and impacts the propulsor. Especially with azimuth thrusters, the transversal load can play a major role. Still, all directional ice loads and magnitudes need to be considered as they hit the propulsor from different sides while the vessel cuts through ice.
When dimensioning arctic propulsors, we at Steerprop analyze the impact of ice loads on the slewing ring dimensioning – the hull attachment inside the ship’s hull, with bolts dimensioned to provide the strength of the housing that withstands the ice loads.
Ice loads also need to be considered when choosing how and in which material the propulsion units should be manufactured. For most ice classes, we recommend stainless steel propellers, but bronze propellers are also available for lighter ice classes. Blade scantlings are calculated according to class rules. The entire propeller can be delivered as a monoblock or built with blades bolted on. In the latter alternative, it is considerably easier to replace a single blade underwater at sea rather than changing an entire propeller.
Pushing and pulling have traditionally been the preferred propulsor type for arctic operations, but recently Steerprop’s contra-rotating propulsion (CRP) technology has been gaining traction with arctic expedition cruise vessels, as the CRP technology combines a robust, durable construction with high fuel efficiency. In addition, electric steering combined with CRP results in smooth operations and outstanding maneuverability. The CRP solution is also silent, it limits propeller noise by having two separate propellers, each with a lower loading, which helps prevent cavitation and lowers both onboard noise and underwater radiated noise.
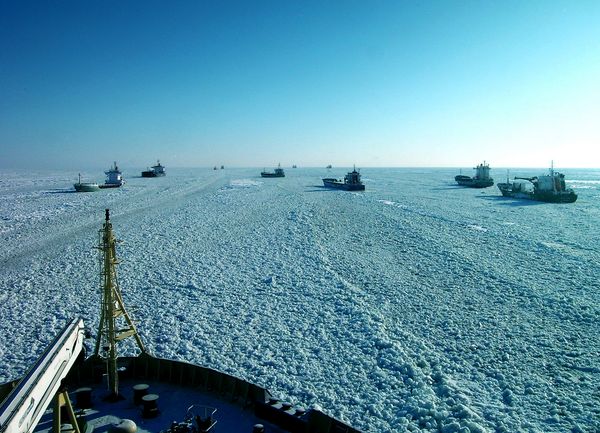
Furthermore, our pollution-free sealing solution for the severe vibration conditions caused by operating in ice has proven effective through experience.
Each ice class affects not only the final propeller design and configuration but also its power transmission gear design and steering. Steerprop uses a unique gear transmission design with the proper and effective load-carrying contact area and pattern that can maintain the safety margin for any unexpected load.
Every Steerprop propulsor also comes with high-quality roller bearings for the very best performance. To maintain consistent quality, we have worked with only two or three top-flight bearing manufacturers over the years.
The most important outcome is to be able to ensure that the vessel can handle even unexpected loads and safely make it through the ice, even if the propulsor is damaged. That’s why we use computerized ice simulations to take the entire line into consideration, including the torsional vibrations from the whole system. We provide our complete analysis of the forces to the ship design house or the shipyard in order for them to further calculate the hull strength needed.
Ultimately, the classification societies set the rules. But it is up to us to calculate, simulate and formulate how much tension and deformation would be allowable at each point in the propulsor for a safe and efficient voyage above and beyond the rules, in the actual arctic marine environment.
Author